THE WORK INVOLVED
THE WORK
1)- Chassis extension & reinforcing;
2)- Suspension fabrication;
3)- Diff axle machining;
4)- Any Bodywork;
5)- Assembly and testing;
6)- Finishing work;
7)- Final testing, certification approval, and registration before customer handover.
In-house work:
All detailed machining and Chassis and suspension work with 2-3 tradesmen (plus apprentice) can produce up to 4 conversions/wk. We have a small machining workshop in our factory with welding able to be accomplished almost anywhere throughout the factory;
Final assembly is carried out in our main factory section.
Supply of Outsourced work:
More specialized operations on some parts are from overseas (Japan & USA). Both genuine factory, and specific aftermarket parts, from domestic suppliers locally.
Conversion work:
First, we strip the base vehicle’s rear suspension and chassis. Then extend and reinforce it.
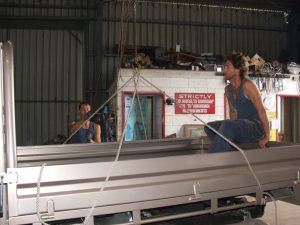
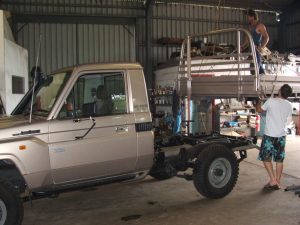
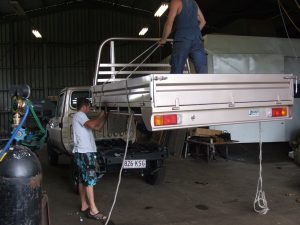
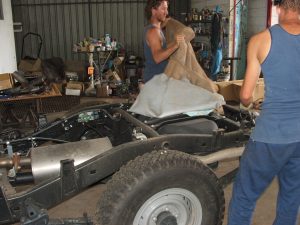
Next we extend and reinforce the chassis to prepare it for our suspension.
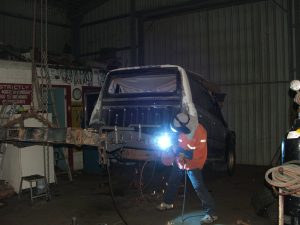
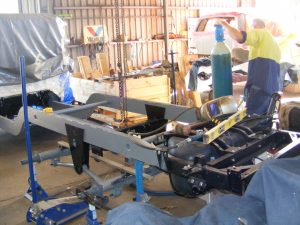
Simultaneously, we source and machine parts for the drive-through diff in our machining shop.
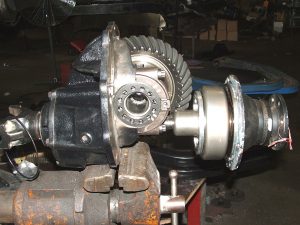
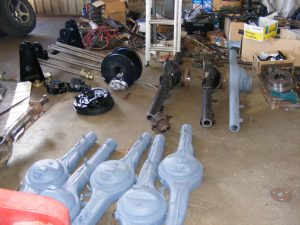
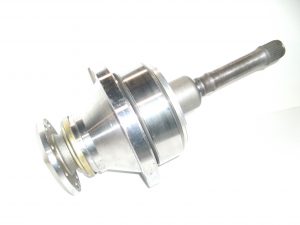
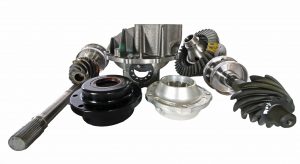

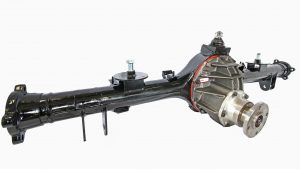
Suspension components are prepared in our welding/frame shop. Seating bushes in place is done before final paint and assembly.
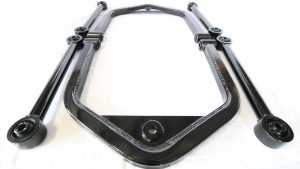
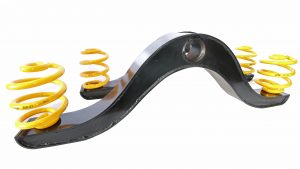
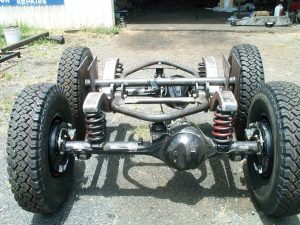
Any bodywork is commenced once chassis is completed. Bodywork is conducted same time as suspension/drive-line begins fitting.
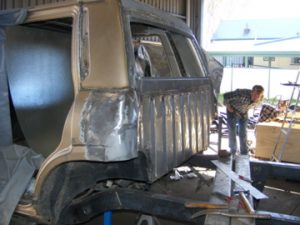
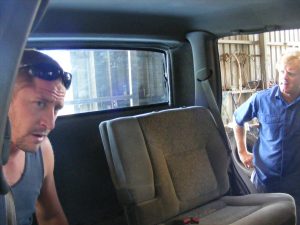
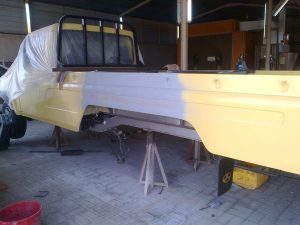
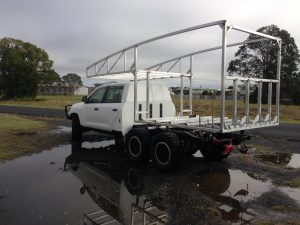
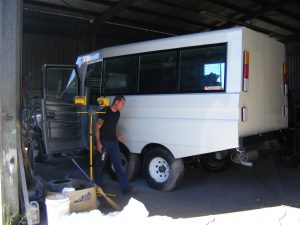
Diffs then get fitted, the exhaust extended, and brake piping finished.
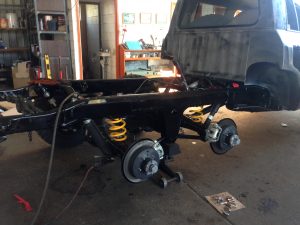
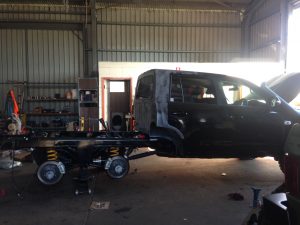
Traybodies and mud guards are now permanently positioned, and tail lights wired up to complete the job ready for certification & registration.
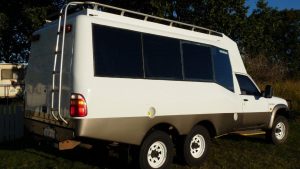
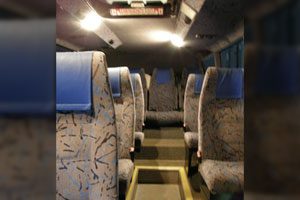
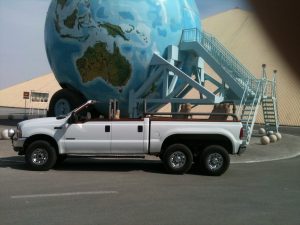